World Class Specimen Tracking
Assist Tracking Provides Exceptional Patient Safety and Delivers World Class Lab Efficiency
Discover why 75 labs (and counting) have trusted Assist Tracking to track millions of specimens and optimize their workflow.
Why Choose Assist Tracking?
Comprehensive & Expansive
Tracking from the moment a specimen is picked up at a clinical site until it’s processed and placed into storage.
Industry Leading
More features and options than any other specimen tracking product on the market. Over 100 billion scanned transactions have passed through the Assist Tracking Engine.
Optimizes Laboratory Operations
A solution that is not tied to a specific hardware of software solution, but is focused on optimizing laboratory operations.
Connect with Us to Learn More
Streamline Your Lab Management with Assist Tracking
Given the complexities of lab workflows, efficient management is essential. Let’s discuss solutions tailored to meet your needs. Email us today at info@assisttracking.com.
Assist Tracking Modules Offer An Unmatched Feature Set
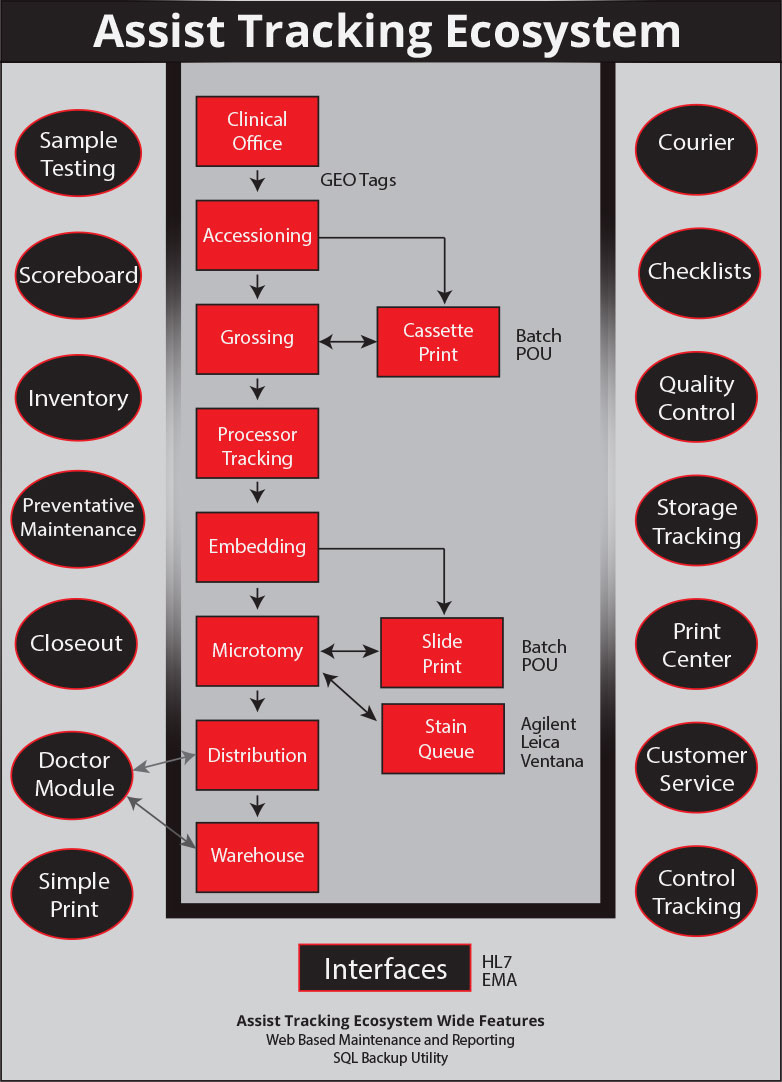
Clinical Office
- Remote office and arrival tracking
- Choose destination lab
- Tracking Manifests – Online, cloud, paper
- Dashboard tracking for pending
- Bi-Directional communications client/lab
- Compatible with EMR (ex. EMA) bar codes
Accessioning
- Ability to print Req/Bottle labels
- Demographic capture if no interface
- Shipping Document capture
- Drives batch block bar code printing
Grossing
- Component Matching – Up to 4 objects
- Point of Use or Batch Scanning
- Compatible with all known printers
- Reprint of blocks via Queue
- Gross notes capture (including dictation)
- Patient Verification Capture
- Communications Log
- Sketch Pad for diagrams
- Image capture for gross pictures
- Specimen Type Protocol defaults
- Clinical Research Project Tracking
- Lot Control tracking
- Checklists/QC Information Capture
- Safety Acknowledgements
- Document Management Integration
Cassette Print
- Hardware Agnostic
- Dropfile vs. Direct Print
Processor Tracking
- Scan Blocks In/Out
- Grossing Batch Release
- Track Equipment and Tissue Runs
- Equipment Downtime Tracking
- Equipment Utilization
- Dashboard Visibility
- Auto Case Holds for Extended Run
- Robotic/Bulk Scan Compatibility
Embedding
- Chain of Custody
- Checklists/QC Information Capture
- Grossing Information Visibility
- Tissue Pieces Visibility
- Case Components Visibility
- Communications Log
- Grossing Notes Visibility
Microtomy
- Point of Use or Batch Matching
- Compatible with all known printers
- No 3rd software for Windows printers
- Automated Specimen type protocols
- Split printing for IHC slides
- Ad hoc stain printing
- Doctor orders for add on stains/recuts, etc.
- Integrated block warehousing
- Checklists/QC Information Capture
- Communications Log
- Equipment Utilization Tracking
- Digital slide queues/worklists
- Tracks at unique slide number level
- Multiple Template views when printing
- Control batch assignment at scan
Distribution
- Tracking of objects delivered from lab
- Distribution and Send outs tracked
- Return Expected vs. not expected
- Automatic Distribution Artificial Intelligence
- Digital Distribution for digital slides
- Compatible with any bar-coded object
Warehouse
- Storage of any objects (ex. Slides, Blocks)
- 7 levels of storage hierarchy
- Integrated pick lists and object pull requests
- Digital Dashboard to track digitizing
- Overdue objects when not returned
- Wet tissue warehouse features
- Tracks offload to 3rd party/offsite storage
- Document imaging for paperwork
Slide Print
- Hardware Agnostic
- Dropfile vs. Direct Print
Stain Queue
- Interface to staining “platforms” (Agilent, Leica, Ventana)
- HL7, XML, File drop compatibility
- Stain rules to route among platforms
Assist Tracking Modules
- Clinical Office
- Accessioning
- Grossing
- Cassette Print (Batch or POU)
- Processor Tracking
- Embedding
- Microtomy
- Distribution
- Slide Print (Batch or POU)
- Stain Queue (Agilent, Leica, Ventana)
- Warehouse
- Doctor Module
- Sample Testing
- Scoreboard
- Inventory
- Preventative Maintenance
- Simple Print
- Courier
- Checklists
- Quality Control
- Storage Tracking
- Print Center
- Customer Services
- Control Tracking
- Interfaces (HL7, EMA)
Module Details
Assist Tracking has over 25 modules that work together to provide the most comprehensive feature set available on the market.
Clinical Office
- Remote office and arrival tracking
- Choose destination lab
- Tracking Manifests – Online, cloud, paper
- Dashboard tracking for pending
- Bi-Directional communications client/lab
- Compatible with EMR (ex. EMA) bar codes
- GEO Tag & Mobile Tracking
Cassette Print
- Hardware Agnostic
- Drop file vs. Direct Print
Microtomy
- Point of Use or Batch Matching
- Compatible with all known printers
- No 3rd software for Windows printers
- Automated Specimen type protocols
- Split printing for IHC slides
- Ad hoc stain printing
- Doctor orders for add on stains/recuts, etc.
- Integrated block warehousing
- Checklists/QC Information Capture
- Communications Log
- Equipment Utilization Tracking
- Digital slide queues/worklists
- Tracks at unique slide number level
- Multiple Template views when printing
Control batch assignment at scan
Distribution
- Tracking of objects delivered from lab
- Distribution and Send outs tracked
- Return Expected vs. not expected
- Automatic Distribution Artificial Intelligence
- Digital Distribution for digital slides
- Compatible with any bar-coded object
Sample Testing
- Full reference lab functionality
- Tracks inbound objects to ensure return
- Handles routing tracking through lab (Ex: Workflow routing: Histology – PCR – Fish)
- Overdue tracking by “sub lab”
Preventative Maintenance
- Full tracking of any/all equipment
- Break/Fix Tracking
- Track Maintenance programs per unit
- Bio-Engineer work lists
- Ad hoc requests for maintenance support – each module can request physical plant maintenance
Checklists
- Elimination of Paperwork
- Quality Control Checks
- Temperature Tracking
Print Center
- Can print all needed bar codes
- No 3rd party bar code applications needed
Control Tracking
- All employee transactions tracked
- Detailed Employee access authorization
- Case Component/Work flow tracking – shows all elapsed time for specimens to transit workflow
- Support for disparate bar-codes – can handle bar codes from other labs via parser
- Slow Bandwidth Support – store/Forward data for remote sites with slow network
Accessioning
- Ability to print Req/Bottle labels
- Demographic capture if no interface
- Shipping Document capture
- Drives batch block bar code printing
Processor Tracking
- Scan Blocks In/Out
- Grossing Batch Release
- Track Equipment and Tissue Runs
- Equipment Downtime Tracking
- Equipment Utilization
- Dashboard Visibility
- Auto Case Holds for Extended Run
- Robotic/Bulk Scan Compatibility
Slide Print
- Hardware Agnostic
- Drop File vs. Direct Print
Warehouse
- Storage of any objects (ex. Slides, Blocks)
- 7 levels of storage hierarchy
- Integrated pick lists and object pull requests
- Digital Dashboard to track digitizing
- Overdue objects when not returned
- Wet tissue warehouse features
- Tracks offload to 3rd party/offsite storage
- Document imaging for paperwork
Scoreboard
- Over 50 visual management dashboards
- Lab metrics, pending counts, etc.
Simple Print
- Printing for remote sites with no network
- Blocks/Slides with template formats
Quality Control
- All employee transactions tracked
- Detailed Employee access authorization
- Case Component/Work flow tracking – shows all elapsed time for specimens to transit workflow
- Support for disparate barcodes – can handle bar codes from other labs via parser
- Slow Bandwidth Support – store/Forward data for remote sites with slow network
Customer Service
- Full customer service integrated features
- Integrated CTI “screen pop” – “Learns” customer phone numbers
- Complaint/Issue Tracking
- Special Handling Requests (ex. Rush)
- Courier Pickup Requests (Ad Hoc)
- Customer Supply Requests (Ex: bottles, requisitions, etc.)
- Special Instructions Capture
- Follow up/To Do lists
Grossing
- Component Matching – Up to 4 objects
- Point of Use or Batch Scanning
- Compatible with all known printers
- Reprint of blocks via Queue
- Gross notes capture (including dictation)
- Patient Verification Capture
- Communications Log
- Sketch Pad for diagrams
- Image capture for gross pictures
- Specimen Type Protocol defaults
- Clinical Research Project Tracking
- Lot Control tracking
- Checklists/QC Information Capture
- Safety Acknowledgements
- Document Management Integration
Embedding
- Chain of Custody
- Checklists/QC Information Capture
- Grossing Information Visibility
- Tissue Pieces Visibility
- Case Components Visibility
- Communications Log
- Grossing Notes Visibility
Stain Queue
- Interface to staining “platforms” (Agilent, Leica, Ventana)
- HL7, XML, File drop compatibility
- Stain rules to route among platforms
Doctor Module
- Doctor Ordering (recuts, stains, etc.)
- Allows for scan tracking
- Ensures licensure eligibility of accessions
- Shows digital work queues
- Supports AI diagnosis visibility
- Peer review functionality
- Detailed Diagnosis/Reporting capability
- Supports multiple LIS environments
- Warehouse requests for objects
- Visibility to Chain of custody/quality
- Doctor control approval tracking
- Lab visibility of doctor orders
- LIS integration and/or Doctor module orders
- Orders can be entered manually
- Order dashboard for lab
- Employee order assignment
Inventory
- Full inventory item receipt/usage
- Lot control tracking of items
- Track employee issuance of items.
- Generate reorder reports with level alerts
- Vendor bar code scanning or generate
- Reagent manufacturing tracking
Courier
- Track specimen pickup from offices
- Courier Route stop tracking
- Air tag support
- Courier Receipt/Confirmation at arrival
- Lock box proof of pickup scanning
- Client Signature pick up tracking
Storage Tracking
- Ability to track specimens into equipment (Ex: Blocks into freezer, specimens in fridge)
- First in/First out alerts to ensure routing – work oldest specimens first
- Allows for “idle” time tracking of specimens
Continuous Innovation
Assist Tracking leads the industry through continuous, progressive innovation. The software goes beyond standard laboratory operating procedures by incorporating additional modules and features, empowering laboratory customers to streamline and enhance their workflows. Driven by client feedback, Assist Tracking continually introduces new capabilities—both those that meet user requests and inventive features that set new standards in specimen tracking.
Architecture & Deployment Overview
Framework
.NET Framework
SQL Server Database
Web-based Reporting
Redundant Database Support
Lightweight Application
Compatibility
Windows XP
Windows 7
Windows 8
Windows 10
Windows 11
Deployment
Equipment Agnostic
Copy/Paste Installation
Supports Various Printers
Shared Monitors/ Scanners
Standard Lab Computers
Label Printing
Direct Printing to Printers
Customizable Menu Visibility
UDI Label Printing
Badge Printing
Label Queue Functionality
Maintenance
Automated Environmental Data Capture
Preventative Maintenance Tracking
Real-time Communication
Customizable Checklists
Extended Serial Number Tracking
Reporting
Visual Management Tool
Scoreboard Graphs
Message/Alert Board
Real-time Refreshing
Customizable Templates
Storage Tracking
Object Placement Tracking
FIFO/LIFO Support
Perishable Storage Management
Offsite Storage Tracking
Non-lab Warehousing
Order Management
Order Closeout Module
Real-time Order Status
Standalone Order Entry
Client Fulfillment
Doctor Module Integration